10 Tips for Patching Drywall
Before you paint a wall you have to prepare the surface, which inevitably involves patching. It’s one of the most important steps. But sometimes it takes more than just a can of spackling and a small putty knife to get good results. Here are some wall patching tips and products that will help you speed up the job, avoid problems and end up with a flawless wall.
1.Use Self-Priming Filler
Patches made with traditional patching materials need to be primed with a sealing-type primer before painting. Otherwise the patched areas could show through the finished paint job as foggy spots. But if you patch with a self-priming patching material, you can avoid this extra step. There are several brands; just look for the words ‘self-priming’ or ‘with primer’ on the container.
2.Use Setting Compound for Big Holes
It’s fine to fill screw holes and other small wall dings with patching compound, but for dime-size and larger drywall repairs, and for holes that are deep, it’s best to use a joint compound that sets up by a chemical reaction. These are available in powder form with setting times ranging from five to 90 minutes. The reaction starts when you mix in the water, and the compound hardens in the specified time. The five-minute version is nice because you can buy the powder in a convenient 5-lb. box, and the compound hardens quickly, so you can apply another coat right away. Remember, setting-type compounds are harder to sand than regular patching materials, so make sure to strike them off flush to the surface when you fill the hole. You’ll find setting-type compounds wherever drywall taping supplies are sold.
3.Make a Dent for the Patching Compound
When you remove a nail, drywall anchor or picture hanger, there is usually a little ridge of old paint or drywall sticking out that’s hard to cover with patching material. The solution is to make a dent over the hole, and then fill the dent. Most good-quality putty knives have a rounded hard plastic or brass end on the handle that works perfectly for making the dent. The rounded end of a screwdriver handle or the handle of a utility knife will also work. Press the handle against the hole and twist it slightly while applying pressure to dent the surface, or if you have good aim, use your denting tool like a hammer.
4.Cover Cracks with Repair Spray
Stress cracks usually show up around window and door openings. The cracks are the result of framing movement and are hard to fix permanently. But using spray-on crack repair is a good way to at least extend the life of your repair. The spray forms a flexible membrane over the crack that can stretch and relax as the building moves.
If the crack is open, fill it first with patching compound. Then follow the instructions on the can to cover the crack with the crack-repair spray. Let it dry and cover it with paint to finish the repair. You’ll find crack-repair spray at hardware stores, paint stores or online.
5.Fill a Row of Holes with One Swipe
Professional drywall tapers always fill a row of screw holes with one long stripe of joint compound, rather than filling every screw hole separately. In addition to being faster, this method disguises the screw holes better and makes it easier to sand the patch. Instead of sanding around each hole, you can just sand the whole stripe.
You can take advantage of this tip whenever you’re filling a series of holes that are lined up and close together, like the holes left from a shelf standard or a row of pictures. Use a 6-in.-wide putty knife and apply the compound as shown in the two photos.
6.Skim-Coat Areas with Lots of Dings or Holes
In areas with a lot of dents and holes, like in the mudroom where boots, hockey sticks and golf club bags leave their marks, don’t try to fill every dent individually. Instead get a wider taping knife—a 6-in.-wide putty knife will do—and simply skim the entire area with joint compound. For the best results, use ‘topping’ or ‘all-purpose’ joint compound.
Mix a tablespoon or two of water into three or four cups of the joint compound to make it easier to spread. Then put a few cups into a drywall pan and use your 6-in. knife to spread it. Spread a thin coat of joint compound over the area. Then scrape it off, leaving just enough to fill the recesses and holes. You may have to apply two or three coats to completely fill holes, but the thin layers dry quickly and are easy to apply. Sand the wall after the final coat dries.
7.Seal Exposed Drywall Paper Before Patching
When you peel off old adhesive or self-sticking picture hangers, you often tear off the top layer of drywall paper, leaving fuzzy brown paper exposed. If you try to patch over this without sealing it first, the water in the patching material will cause the paper to bubble and create an even bigger problem. The key to patching torn drywall paper is to seal it first with an oil- or shellac-based sealer (KILZ Original and BIN are two brands). These are available in spray cans or liquid that you can brush on. Don’t use a water-based product or you’ll likely have the same bubbling problem. After the sealer dries, sand the area lightly to remove the hardened paper fuzz. Then cover it with patching compound as you would for any other wall repair.
8.Use Stick-On Patches for Midsize Holes
There are all kinds of ways to patch doorknob-size holes. But the quickest and easiest is to use one of these stick-on mesh patches. They’re available in a few different sizes at paint stores, hardware stores and home centers. To use the patch, just clean the wall surface and sand it to give the surface a little ‘tooth.’ Then stick the patch over the hole and cover it with two or three thin layers of joint compound. You can speed up the process by using setting-type compound for the first coat.
9.You Can Spray on Wall Texture
Orange peel texture on walls or ceilings is nice for hiding defects and adding interest, but it can be a real pain if you have to make a big patch. Luckily you can buy spray-on orange peel patch that will allow you to match the texture of the patch without hiring a pro. You can buy the patching material in a few different versions: regular, quick-drying and pro. The pro version gives you the most control over the spray pattern.
Make sure to practice spraying the texture onto a scrap of drywall or cardboard to fine-tune your technique before you spray it on the wall patch. Let the test piece dry before you decide whether you need to adjust the nozzle for a coarser or finer texture. Remember, you can always add another coat if there’s not enough texture after the first coat dries.
10.Use a Raking Light When Patching Walls
When you’re preparing your walls for paint, position a bright light so that the beam rakes across the wall as shown here. This will accentuate any defects, making them easier to see and fix, and will alert you to patches that need more fill or additional sanding. If your walls look smooth in raking light, you can be sure they’ll look awesome when you’re done painting.
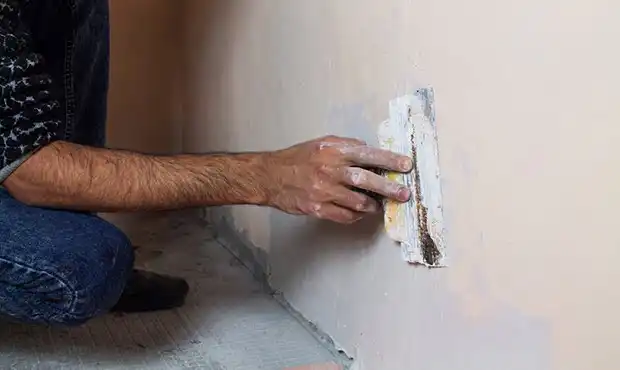
Here’s how to repair and patch damaged drywall
No matter the age of your home, drywall damage will occur. Whether it be from doorknobs, roughhousing, minor water damage, moving furniture or mounting hardware from artwork, mirrors, TV mounts, window treatments, etc., it will happen. Minor damage is a relatively easy fix. Small screw or nail holes can even be patched with white toothpaste and touch painted to blend in.
Repairs to areas of major water damage are best left to the pros. You never know what kind of damage is lurking behind that drywall. There could be mold and that is something that is best left to a professional mold remediation expert.
The age and condition of the paint on your wall and stored paint from when it was applied are really the key factors in how quickly you will finish drywall repair projects. But it’s the quality of the patch work that is critical to restoring drywall to look like new. The paint will only look as good as the surface it’s applied to. A poor patch with a poor texture match will stand out more than you’d expect, even with the best paint coating.
Nail holes in a wall where a picture used to hang can be filled with spackling paste, caulk or even toothpaste for an especially tiny hole; let it dry and sand it down before repainting.
For dents or holes larger than a quarter, drywall texture and drywall tape or mesh will be required to complete the project. Anything over a 2-inch square will require a scrap drywall piece to cut a filler piece along with the following tools:
Utility knife or drywall saw. Having both can come in handy, but you won’t need both if you only own or have access to one.
- 12-inch straight edge.
- A level.
- 4-inch putty knife.
- Coarse sponge or sandpaper.
Optional:
- Acrylic caulk if the patch is matched up to another material/surface such as a countertop, shower, tile finish, etc.
- Drywall pan if a large amount of mud will be required.
- Texture spray for orange peel finishes.
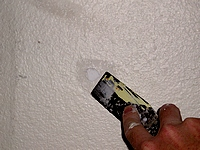
Pro Tip: How to Repair Torn Drywall Paper
So you finally got around to removing that paneling or tile and RIP! Off comes some drywall paper (also called facing) along with it. Now what started as a fun update project has turned into an annoying repair project. The damage isn’t deep, but it’s unsightly. So what’s the right way to repair it? Well, why don’t you ask us a hard question? We’ve tackled patching a hole in drywall, and this will be easier than that. How to repair torn drywall paper and patch it up is a Pro tip you’ll want in your back pocket.
Well That’s Not Tearable
- Remove loose paper with a razor knife.
You’ll surely have some ragged or hanging paper left from the tear, so use a razor or utility knife to remove it. The edges of the tear should be smooth against the wall.
- Important: seal the exposed gypsum.
The gypsum will absorp moisture from latex paints, so you must seal it to prevent blisters. You can use some drywall primer and sealer or even old oil-based paint that you told yourself you’d use or throw out but haven’t done either.
- Cover the area with joint compound.
Use a putty knife to spread a thin layer of joint compound (mud) over the area. You’re not just filling the torn area, you are creating a new surface so the joint compound should extend an inch or so past the edges of the tear. Apply the mud as evenly as possible but you’ll find that it may look uneven or pock-marked, especially if you’ve never done this before. Not to worry – read on.
Last Steps: Repair Torn Drywall Paper
- Sand the area.
It’s common to use a fine sandpaper such as 120 grit to sand the area. For larger areas you can turn to a bigger tool like the Ridgid Gen 5X random orbit sander. We’ve even used a multi-tool with a sanding accessory. However, we prefer a wet sand before the joint compound has completely cured. A wet sand doesn’t create fine airborne particles or dust on floor, and it gently removes the area’s high spots and fills the low spots. The curing time depends on temperature and humidity, but we like to give the area around 45 minutes to harden up. Touch the compound to make sure it’s not so wet that it comes off on your fingers. It should be firm but pliable. Use a damp sponge to gently sand the area and create a smooth surface with the rest of the wall.
- Apply another layer of joint compound.
What’s better than one layer? Two, of course. A second layer will likely be necessary to make the mud coverage wide and smooth enough to blend in. You’ll never notice the area once it’s painted if you do it correctly. You’ll likely want to repeat the sanding step as well.
- Paint.
Here’s where the evidence of the tear disappears. Paint the area, and enjoy that invisible repair.
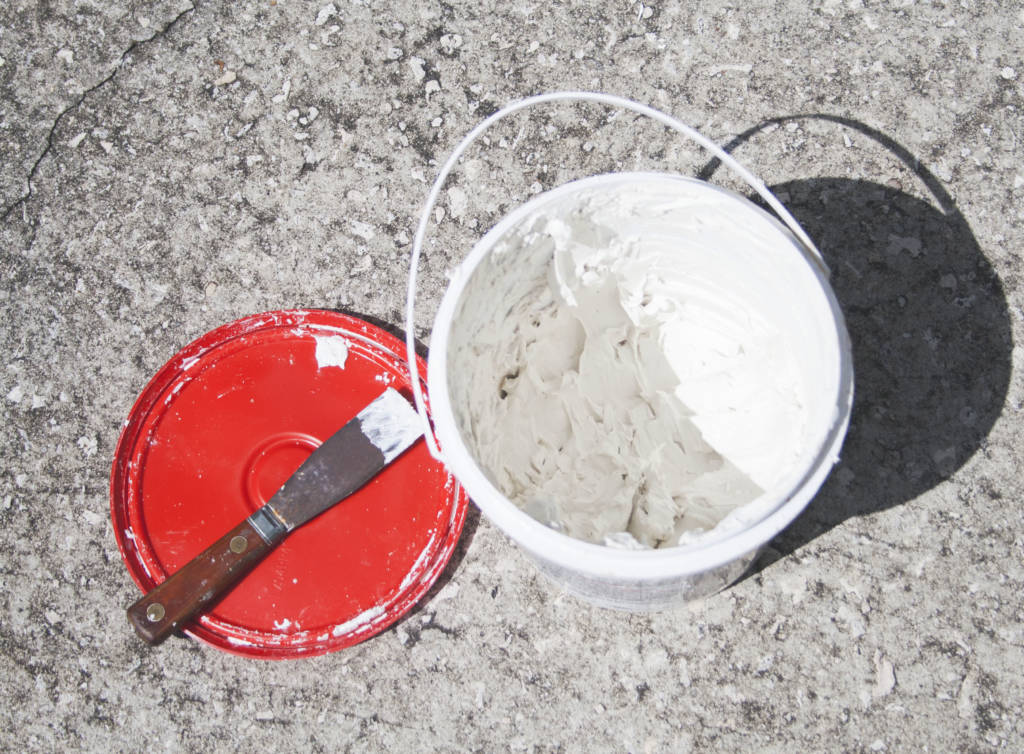
Drywall Repair – A Common Problem In Every Home
A common problem in almost every home is drywall repair. Anytime we are indoors we are usually surrounded by drywall – a less than perfect building material. It’s fragile, is easily ruined by a bit of water and can be a magnet for mould. Yes, there are water-resistant varieties now, but drywall can still be miserable. Just think of the first time you tried hanging a picture before realizing it’s not that simple on drywall.
However, we have not come up with anything better. It’s been around for decades, having replaced plaster. Plaster had far worse drawbacks. Among them, it takes forever to dry and is much more labor-intensive to install.
Drywall was a great idea because it’s like applying plaster except most of the messy work is done in a factory, and it’s shipped to your home ready to install. Before you know it the job is done, and only later do you realize that you tackled one of the most dreaded jobs of home remodeling. Repairing drywall is even easier.
No matter how well drywall is hung and finished, eventually it will need repairs. Daily life brings about all sorts of wear and tear, like doorknobs creating small holes in walls. Even if every adult, child and pet is a perfect family member and each manages to not cause any damage, natural processes will still slowly take hold.
The rigid materials that give our houses their structure eventually start to shift due to natural expansion and contraction. Drywall will crack. There’s no need to be anxious. Even extensive drywall damage is fixable, even if it means replacing large pieces. Most drywall repairs require just basic skills, tools and drywall patching mud.
Joint Compound vs Spackle, Which One Should You Choose?
Joint compound and spackle are two fantastic products that are designed to help you fix the imperfections on the walls in your home. However, when faced with the decision of having to pick between the two, which one should you choose?
Although personal preference definitely plays a role, it really comes down to what you’ll be doing with it. Before we continue though, it’s important to have a good understanding of what joint compound and spackle are.
Joint compound, also called drywall compound, is a putty that has the consistency of plaster and is designed for larger jobs. Joint compound is made by mixing gypsum dust and water into a paste. It’s usually comes in a pre-mixed container for your convenience and is commonly used for taping and finishing drywall seams. There are 4 kinds of joint compounds on the market. They include:
- All-purpose compound: Can be used for all phases of the patching process.
- Topping compound: Made to be spread on a wall with two dried coats of taping compound.
- Taping compound: The first and second coat of compound you want to put on.
- Quick-setting compound: Made to dry faster than the other compounds and works great for deep cracks and wide holes.
Spackle on the other hand is a name brand product made by Muralo Company. It resembles paste and comes in lightweight spackle and heavy spackle.
Lighter Spackle is generally made from vinyl and used to smaller fill holes made by nails, pins, and needles. Heavier spackle is made from acrylic and typically used for larger, thicker holes.
Spackle also is sold in pre-mixed containers for easy use, but for those that are interested, powdered mixes are also available. To keep the powdered mixes from going bad, make sure you only mix enough for the job you’re about to do